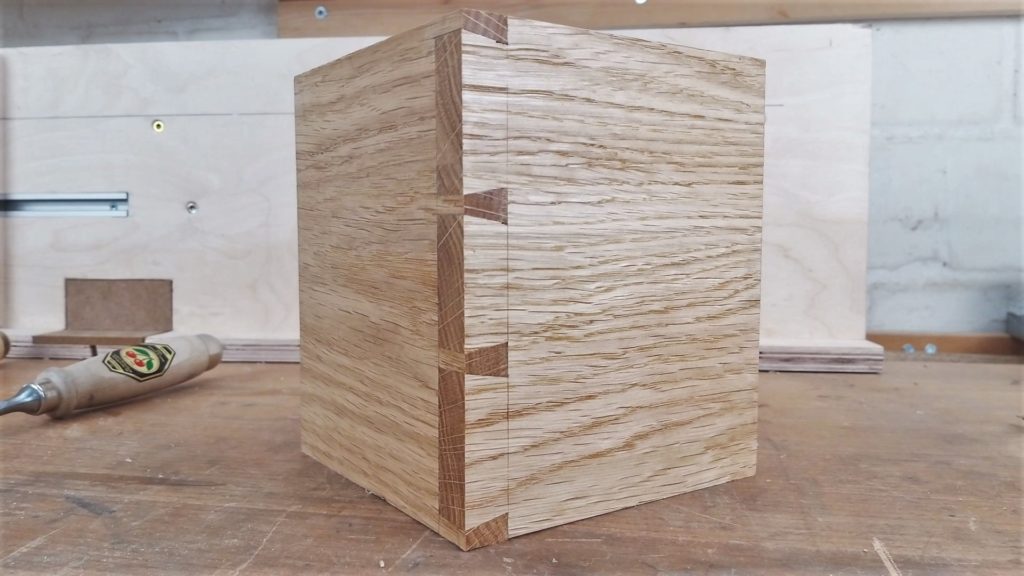
A fast method with a hand-cut dovetail look
No doubt, hand-cutting dovetails is a super cool skill to have. But when you have to cut a lot of dovetails the same size, like multiple drawers, hand-cutting gets tedious, time consuming and repetitive.
This method on the table saw gives you dovetails with that hand-cut look (narrow pins, wide tails), is totally flexible in terms of the angle as well as spacing of the dovetails and gets you there in almost no time.
Tools you need
- sliding bevel*
- narrow chisel* to get into the pinholes
- marking knife
- flat-top grind table saw blade* (optional)
- dovetail marker (optional, you can use the sliding bevel)
Material list
- 15mm (½”) birch plywood
- 50 cm (19½” ) long t-track
- 2 t-slot nuts
- 2 male M6 star nubs
- 2 threaded inserts (optional, you can also use wood screws to attach the jig to your miter gauge)
How the jig for dovetailing works
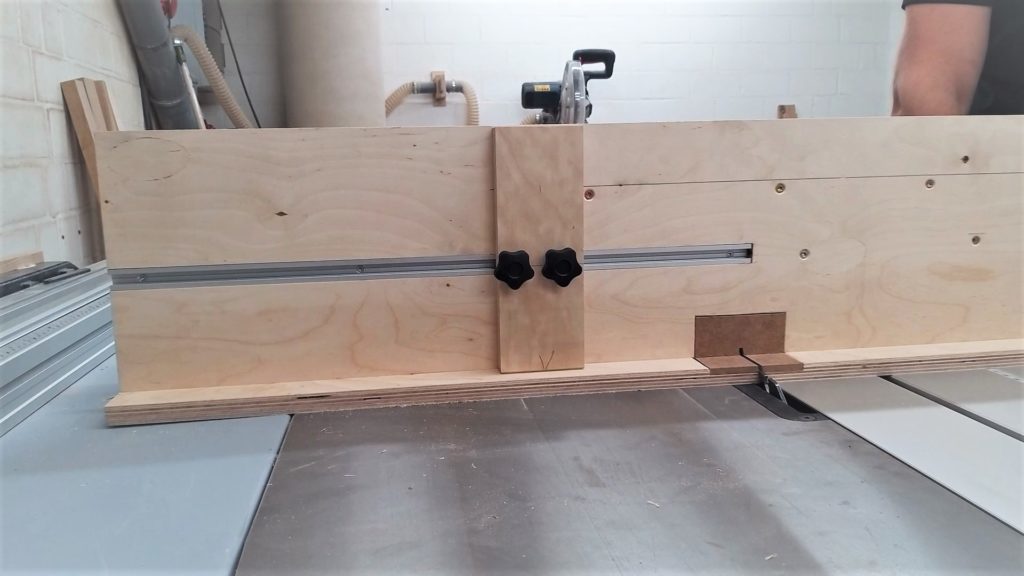
The jig is simple and is attached to the miter gauge of your saw blade. The angle for the tails is achieved by tilting the blade and the angle for the pins by adjusting the miter gauge. The stop block ensures perfect repeatability of the cuts on multiple boards. With MDF inserts you get tear-out free cuts every time.
Building the jig to cut dovetails on the table saw
I start by ripping 15mm (½”) birch plywood to a 20cm (8”) strip and two 5cm (2”) strips. The length of these pieces determines how much support of the workpiece you have on either side of the blade. In my case, I wanted to be able to make dovetails on boards at least 40cm (16”) in width. Therefore I needed 40cm (16”) on each side plus an additional 7cm (2¾”) in order to accommodate for the stop-block. That means my boards have to be 94cm (37”) long.

Into the board for the back and the board for the base, I routed a 5cm (2”) by 8cm (3”) wide recess with a depth of 6mm (¼”) in the center of the board. This recess will accept a 6mm (¼”) MDF plate that gets screwed in from the back and acts as a zero clearance insert. Thereby you just have to change out the MDF piece, when you change from tails to pins. It also makes it possible to cut different dovetail angles with the same jig.
When you make the MDF inserts make a whole lot of them right away since you will need 4 every time you cut a batch of dovetails. The inserts don’t have to fit gap-free or whatsoever.

Time to route the slot for the t-track. The track only has to be on one side of the blade. The height of the track in the jig should be higher than the maximum cut height of your table saw. Then I cut the t-track to length, countersink, pre-drill and screw it in place.
In order for the back to stay flat, I screw one of the 5cm (2”) strips to the back. The other strip gets attached to the bottom of the jig. It is flush with the side that gets connected to the miter gauge and sticks out in the front. The workpiece will rest on this strip, when making the cuts. Make sure it is perfectly perpendicular and don’t place a screw in the spot where the blade is gonna cut. I almost did…

Alright, the jig is almost finished. But it still needs a stop-block to make the cuts repeatable. I 7cm (2¾“) wide and 20cm (8”) high piece of 15mm (½”) birch ply takes care of that. With two holes for M6 star knobs, you can mount it to the t-track. The stop needs to be square to the base of the jig.
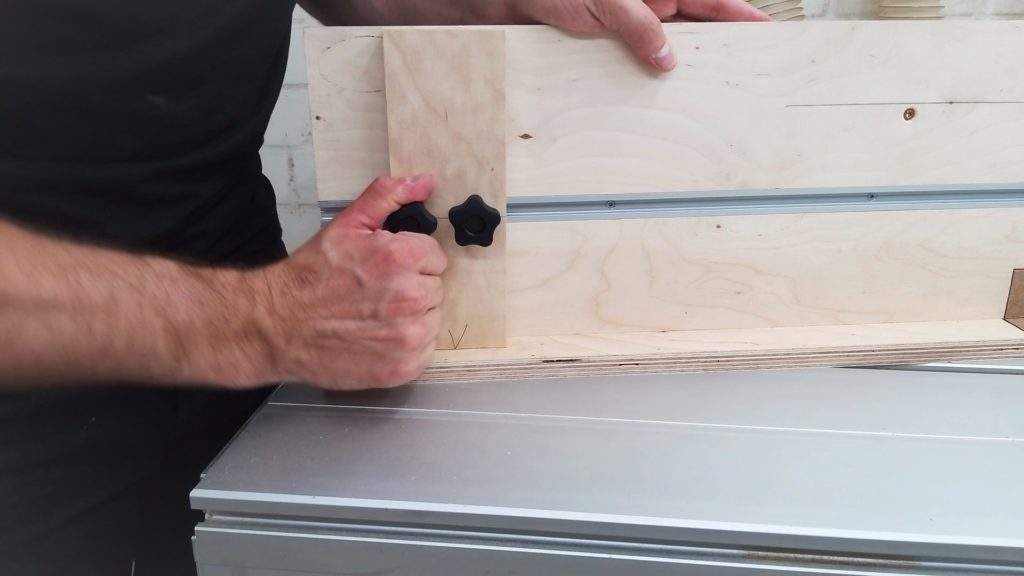
Now the jig is ready to be attached to the miter gauge. How really depends on your particular miter gauge. For my sliding table saw I had to drill two holes to accept the pins of the gauge and place two threaded inserts for the M6 star knobs.
The process of cutting dovetails on the table saw
Layout
Time to cut some dovetails.
First I mark my outside faces with a scribble and label them with pins and respectively tails.
Note: When you batch out dovetails on multiple boards with the same width, at which this method really excels, you only have to make the layout on one board.
After that, I set a marking gauge to the thickness of the boards and strike a line across both faces of both boards. On the tail board I also mark on the edges.
With a dovetail marker and a pencil I layout the tails and mark the pins as waste.
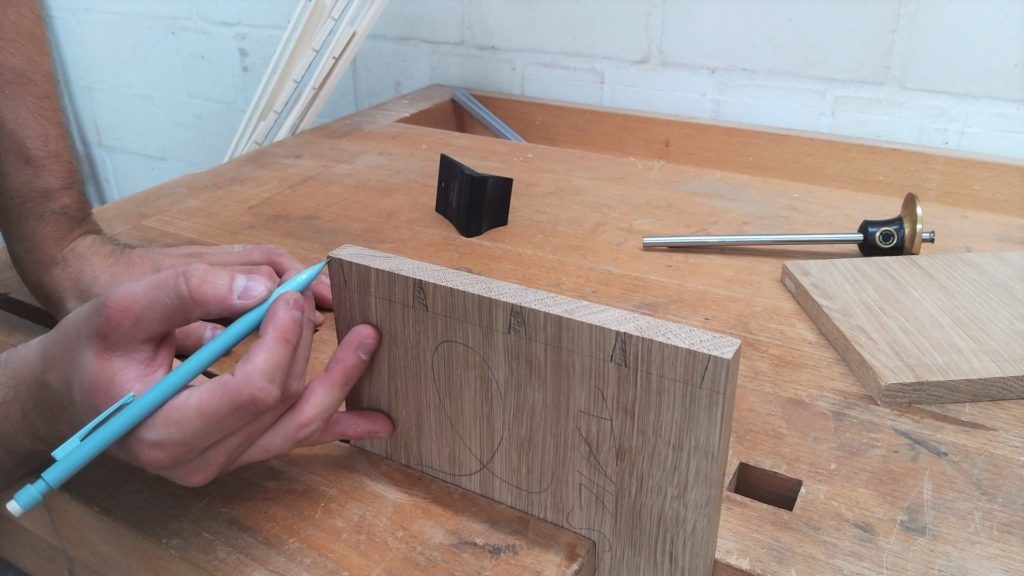
The thickness of the pins at the narrowest point has to be at least the thickness of your saw blade. With a thin-kerf blade you can go super narrow.
(You can also use your sliding bevel set at the desired angle for this step)
Then I set the sliding bevel to the exact angle of the dovetails.
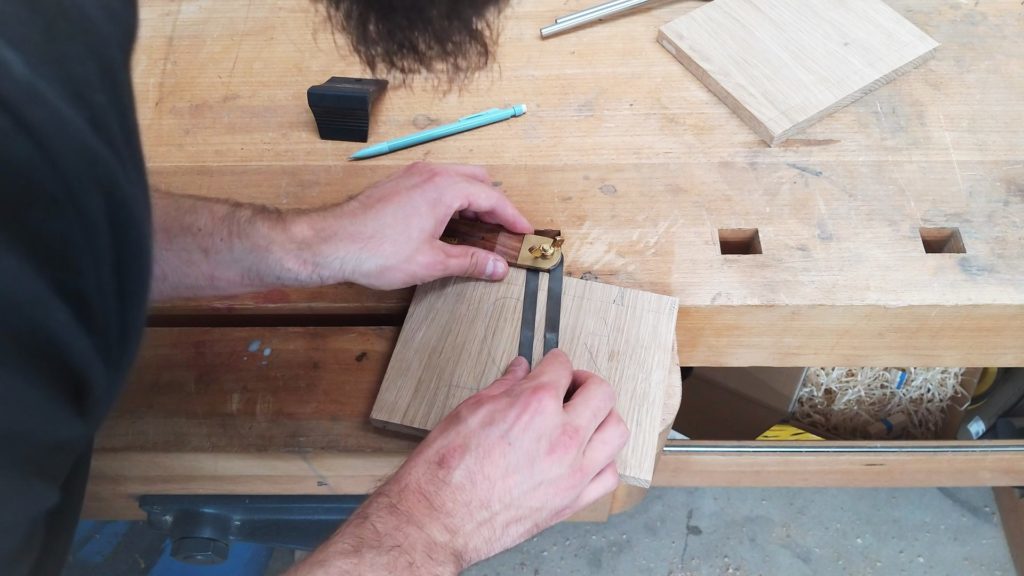
Cutting the tails on the table saw
The sliding bevel now can be used to tilt the blade to the exact angle. The jig has to be attached to the miter gauge and set to 90°. In order to dial in the exact height of the blade, I use a scrap piece with the same mark as the real boards.
After the height of the cut is set up I can position my board for the first cut. Before I make the cut I slide my stop-block in place and lock it. This makes sure the position of the cuts for the other boards will be exactly the same.
If you want to chisel less on the tails, you can buy a custom blade with the correct dovetails angle at the top of the teeth. This leaves almost no waste in between the tails.
With a standard blade, I want the teeth to almost touch the line at the highest point.

I flip the board face-to-face to make the cut on the other side. By flipping it is not necessary to tilt the saw blade in the other direction.

After I have repeated the process for all the cuts on the tail boards, I chop out the remaining waste between tails with a chisel and a mallet. With a Japanese pull saw and a chisel I remove the rest on the sides.
Before cutting the pins I insert new MDF plates in the jig.
Layout and cut the pins
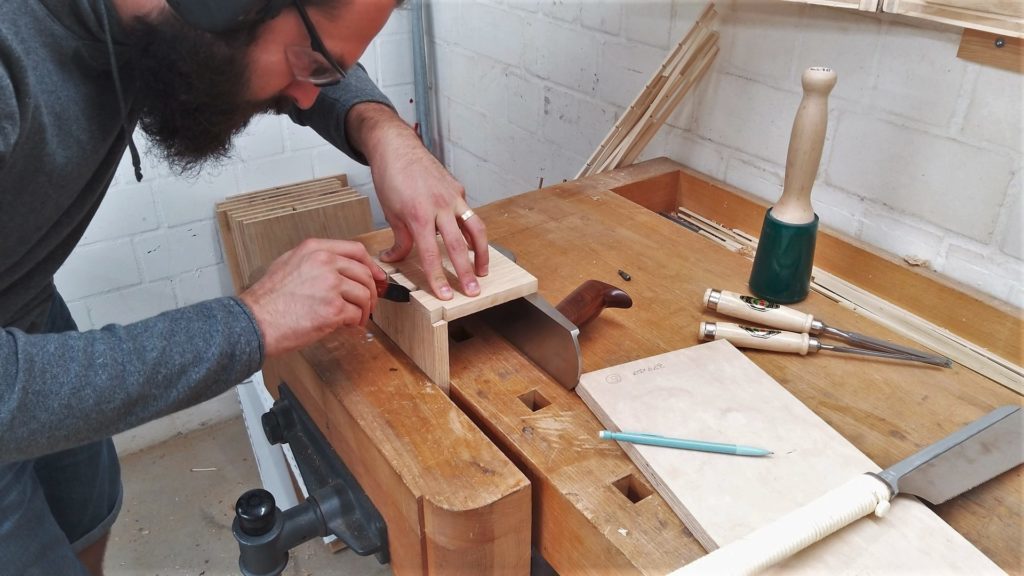
For marking the pins I like to use a marking knife. With a small combination square, I can transfer the lines to the front, since the end-grain is not visible when aligning for the cut. I also mark my waste.

With the sliding bevel still set to the correct angle, I now align the miter gauge.
Again with a piece of scrap, I dial in the height of the blade. Now I want to hit my scribe line dead on.
Then I make all of my cuts on one side of the pins. When batching out, I lock the stop block and make every cut for the different boards and then move to the next setting.

Do not flip the pin board face-to-face like the tail board. It doesn’t work and you end up with a cut in the wrong direction. You can guess how I found out.
With a second cut right next to each first cut I remove a little bit of waste. This is not possible later on with the miter gauge shifted in the other direction because you would end up cutting into your pin.
In order to cut on the other side of the pins I set up the miter gauge in the other direction and make the respective cuts.
As the last step, I nibble away the remaining waste with a series of cuts.
Now it’s time for a test-fit!
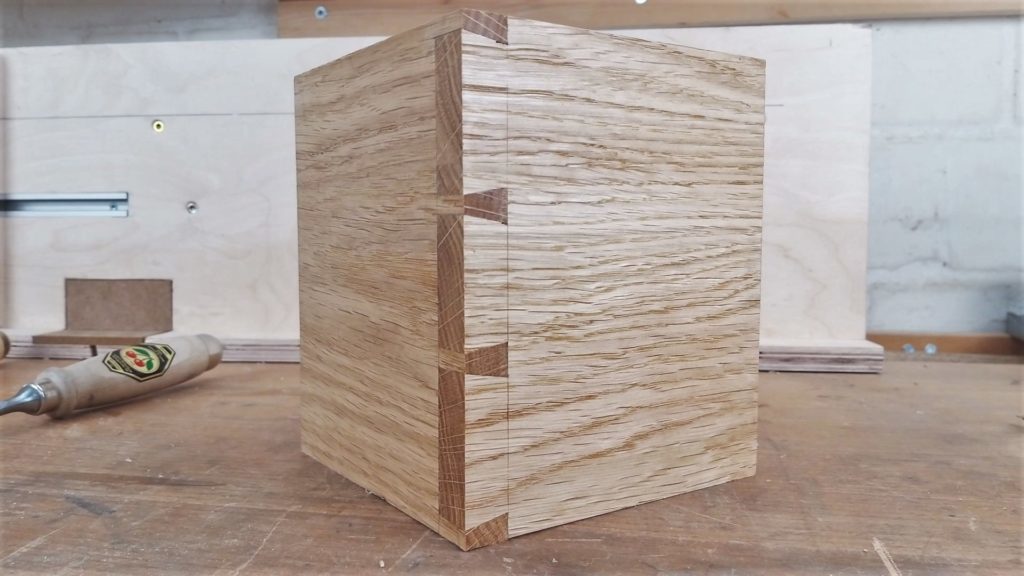
Summary
I found this method for cutting dovetails on the table saw gives you speed and repeatability while still obtaining the narrow pins and wide tails.
Further, you only have to lay out the tails and pins on one board and the other boards end up perfectly the same, thanks to the stop block.
The MDF inserts make the jig flexible in terms of the saw blade and angle you use.
Sure it is not as fast the router method but the result is way more beautiful.
What do you think? Have you tried this method? How did it turn out? Let me know in the comments below!